Corrosion Protection
Providing corrosion and abrasion resistant liners for pipe, vessels
and other process equipment.
We help your company stay in production uptime by providing corrosion and abrasion resistant liners for pipe, vessels and other process equipment. We use thermoplastic resins and a process called rotational lining to create a long-lasting liner inside vessels and pipe with complex geometries, large diameters, and lengths up to 20’.
If you are looking for corrosion protection for applications with electronic chemicals, semiconductor, or other high purity uses, additional information can be found here.
The main industries we serve are chemical processing, mining and fracking, oil and gas, water handling, and desalination. We install thermoplastic liners in pipe, tanks, pressure vessels, scrubbers, fittings, pumps, valves, flowmeters, filter housings, heat exchangers, and other process equipment. We also pride ourselves in offering custom solutions, so if you do not see your specific application listed here, please contact us to discuss your project.
Advantages of Rotational Lining For Corrosion Protection
Rotational Lining Protects equipment against:
- Mild abrasion
- Aggressive, corrosive materials such as:
- Acids (hydrochloric, hydrofluoric, nitric, sulfuric)
- Caustics (sodium hydroxide)
- Sulfides (hydrogen sulfide)
- Halogens (chlorine, bromine)
- Brine and seawater
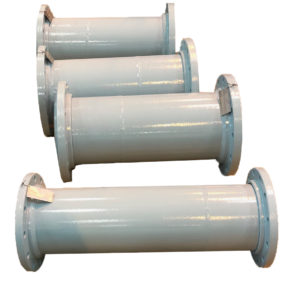
Advantages of Rotational Molded or Laser Sintered Ducts Compared to Composite, Aluminum, or Extruded Ducts:
Seamless liners eliminate failure prone weld joints, which results in increased service life.
Complex parts are easily lined without direct access to internal surfaces.
Mechanical bond eliminates need for adhesives, reducing risk of delamination of liner.
Liners can be completed in less than a week, even with complex shapes.
Durable thick liner (0.450”) offers abrasion protection, impact resistance, and corrosion protection against most chemicals.
Roto-lined equipment has a low operational cost and decreased maintenance for the end user.
What makes our Rotolining Manufacturing process different?
- Value add services to save you time and eliminate additional expense
- Rigorous testing to ensure your product is compliant
- Quality control for your product, operating under ISO 9001-2000 and AS9100:2016
- Flexibility to meet your rigorous installation deadlines
- Tailored solutions to meet your specific needs
- Guidance to help you choose the best material for your application
- We have been rotationally lining both small and large process equipment for over 30 years
Companies We Work With:
Shell Global, Occidental Chemical Corporation, DowDupont Inc., The Chemours Company, Westlake Chemical, ExxonMobil, OneOK Inc., Enterprise Products, and others.
Designing for Rotational Lining
Rotational [...]